What Is Ultrasonic Non-Destructive Testing (NDT)?
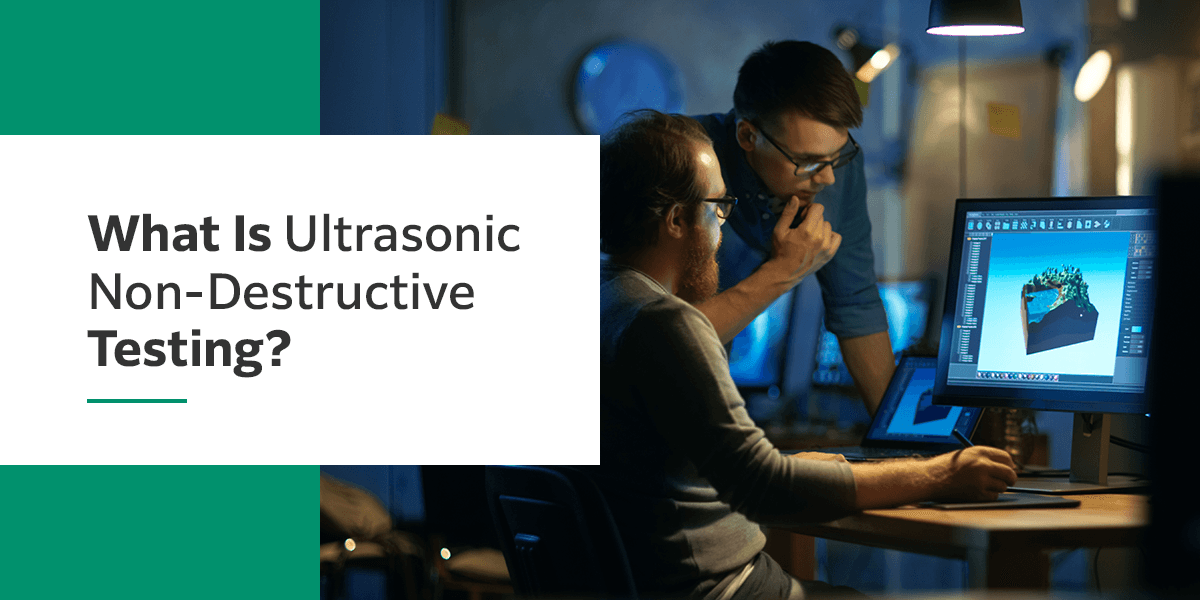
Although ultrasonic technology often conjures up images of a doctor’s office, its original purpose back in the 30s was to detect defects — an application of ultrasonic technology that’s still in use today. Ultrasonic testing is a versatile method of non-destructive testing (NDT), meaning it won’t damage or alter the item. It doesn’t damage components, use radiation or even require access to the entire item, making it a particularly useful technology to have on your side.
Let’s explore the mechanics of this technology and what ultrasonic inspection is used for.
How Does Ultrasonic Testing Work?
Ultrasonic testing uses a transducer to send high-frequency, short-pulse sound waves through an object and pick them back up at a receiver. Based on how those sound waves bounce and move through the material by the time they reach the receiver, operators can detect flaws and identify characteristics of the material. This method can be used to measure thickness, look for irregularities and monitor the condition of flaws, among other uses.
Ultrasonic non-destructive testing can be done in several different ways, each of which uses a piezoelectric transducer. This device converts acoustic energy into electrical energy and vice versa. It essentially generates the acoustical energy that moves through the item. When the energy hits a discontinuity in the material, some of the acoustic energy bounces back for a receiver to pick up. A flaw detector — a type of receiver — identifies these anomalies and displays them on an oscilloscope, which displays the signals graphically and requires a trained operator for interpretation.
Transducers can use one of two types of configurations, including:
- Pulse-echo: In this design, the acoustic energy is both emitted and received in the same transducer. Pulse-echo is the most common option, as it is simple to set up and more portable. If the signal hits something, such as an imperfection in the object, the waves bounce back to the probe. The probe interprets the waves and shows how the signal moved through the material. This is the best option for large items where it’s difficult to reach the other side.
- Through-transmission: With through-transmission, the object being inspected sits between an emitter and a receiver. The emitter sends the waves through the object and toward the receiver. Any imperfections affect how much sound the receiver picks up. This option is better suited to small items.
Another notable component of ultrasonic testing is the couplant. Gel, oil or water are some typical couplants, and they all help to transmit the sound energy from the transducer to the object being inspected. The couplant displaces the air between the transducer and the surface so the sound waves can more effectively pass through them.
Types of Ultrasonic Testing
Ultrasonic testing comes in a few varieties, primarily contact testing and immersion testing, which each offer advantages in different situations.
Contact Testing
Ultrasonic contact testing is the more portable option, great for large or hard-to-reach items. It uses a pulse-echo transducer and a couplant, and the transducer requires contact with one surface of the item. They’re useful when only one side of the material can be reached or the item is oddly shaped. Plus, you can bring the transducer to the item, instead of the other way around — great for items difficult or costly to transport.
Immersion Testing
Another option is ultrasonic immersion testing, which is better suited to a lab or factory environment. This strategy is often used when the item has a complex shape or curves. The object is placed in water, which functions as the couplant. The pulse-echo method is also used here, with a single probe emitting and receiving the wave information.
What Is Ultrasonic Inspection Used For?
The applications of ultrasonic testing in NDT environments are wide-reaching, accomplishing tasks like quality assurance, lab research and periodic testing. These tests can provide information on characteristics like material thickness. They can even be used as a monitoring method to keep an eye on known flaws over time and ensure they don’t grow or corrode further. NDT can be fundamental in preventing total and component failure. It can identify flaws such as shrinkage cracks, laminations, holes, stringers and more.
Some of the industries that rely on ultrasonic testing include:
- Aerospace
- Automotive
- Medical
- Construction
- Oil and gas
- Rail
- Metallurgy
- Manufacturing
Workers in these industries can use ultrasonic testing with many different materials, but some provide better results than others. Materials commonly used in ultrasonic testing include metal, composites, plastic and ceramic. A high density improves the accuracy of the image because it causes less attenuation, and many products that aren’t particularly dense are still well-suited to this technology. Paper and wood are some of the few materials that ultrasonic testing isn’t suitable for, along with coarse grains like cast iron that can reduce sound transmission.
Users turn to this type of testing for a few different reasons, such as:
- High penetration power: Ultrasonic testing can detect flaws deep under the part’s surface as well as surface-level flaws.
- High accuracy and sensitivity: This method offers greater accuracy than many other types of NDT, providing strong sensitivity and reliable results.
- Safety: Ultrasound is often preferred in medical environments because it offers a better safety profile than imaging methods that create radiation or require contrast dyes. Testers outside of the medical field like it for the same reasons. It doesn’t expose nearby workers to radiation and limits the need for additional materials that could discolor or destroy the item.
- Flexibility: Since the system is portable and can be used when just one side of the item is available, ultrasonic NDT allows for greater flexibility and adaptability. You can bring it to various sites and use it on large, hard-to-reach components. Plus, with immersion options, you can test complex components with a wide range of characteristics.
- Quick preparation and immediate results: Ultrasonic inspection is also popular because of its minimal prep work. Simply applying a couplant is often all that’s required. And with quick results, you can make decisions faster with all of the information at hand.
- Automation: Ultrasonic testing can be automated in many systems, making it a great efficiency booster, particularly in environments like manufacturing plants or standardized inspections.
Choose Fujifilm for Your NDT Needs
When it comes to NDT, Fujifilm builds some of the industry’s most trusted devices. We’ve been innovating for decades, bringing imaging expertise to the NDT field for superior results. We can also help you implement assisted defect recognition (ADR), an incredibly valuable tool that can help you automate more of your NDT processes.
Our ultrasonic inspection devices can accomplish a range of tasks with ease and accuracy. Get peace of mind knowing that Fujifilm is helping you ensure quality components. To learn about our ultrasonic NDT devices, get in touch with a representative today.