What Is Visual Testing in NDT?
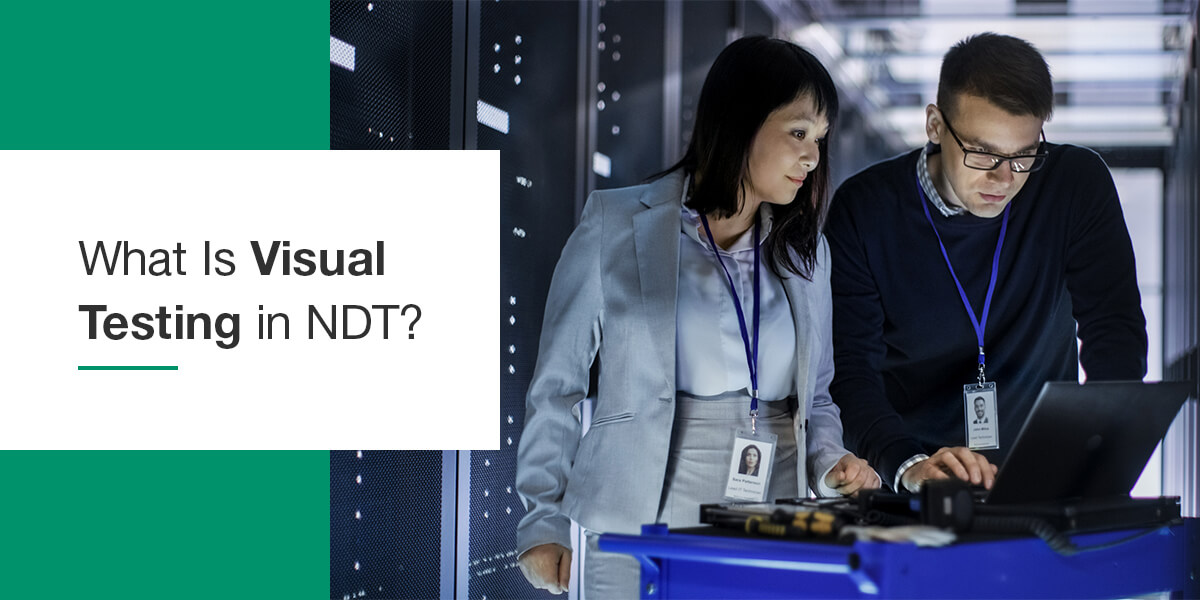
There are several terms for visual testing (VT), such as non-destructive and visual inspection, nondestructive evaluation, nondestructive examination, VT inspection and visual testing examination. Non-destructive testing (NDT) refers to information collection processes that avoid harming or permanently modifying the structure being inspected.
Out of all the nondestructive testing methods, visual testing is the most popular because it’s easily done, low cost and does not require a lot of expensive equipment. Visual testing is used to find surface discontinuities, which is done with the naked eye.
Some equipment you might use with visual testing includes mirrors, magnifying glasses and boroscopes. If the component you’re working with can in fact be viewed, that is the first step in the NDT examination. Some examples of components that might go through visual testing for degradation or corrosion include pressure vessels, boilers, welds, piping and storage tanks.
How Does Visual Testing Work?
Visual testing is used to observe a component’s condition so that the part can be assessed as a part of a maintenance process. Technicians use visual testing to find out if something is wrong with a component and if it needs maintenance. Below are some examples of what an inspector doing a visual exam might be looking for if they were performing a visual testing procedure for an industrial boiler:
- Cracks in the welds holding the boiler together
- Leaks or other integrity issues concerning the boiler’s floor or walls
- Corrosion on the sides of the boiler
- Problems with any of the supporting equipment that helps make the boiler run
Ultimately, visual testing is used to fix challenges like these before they become more difficult to work with and cause additional problems for a business, such as increased costs.
If an inspector performing a visual test misses an issue with a component, such as corrosion on the sides of the boiler, a serious accident could happen down the line. Visual inspections are crucial, especially for assets like pressure vessels and boilers that receive examinations by professionals who follow rigid guidelines mandated by law.
Types of Visual Inspection
There are various types of visual inspections, which we will explore more deeply below:
- Ultrasonic testing (UT): Ultrasonic testing is a process where changes in the material’s properties are located through the transmission of high-frequency sound waves.
- Radiography testing (RT): Imperfections are identified with radiography testing through gamma- or X-radiation.
- Magnetic particle testing (MT): Magnetic particle testing examines disruptions in a material’s magnetic flow to identify any imperfections in a component.
- Acoustic emission testing (AE): A component’s defect(s) can be located with acoustic emission testing by using acoustic emissions.
- Liquid penetrant testing (PT): Liquid penetrant testing is also referred to as dye penetrant testing, which is when a technician uses a liquid to coat a material. After the material is coated, the technician will locate imperfections by identifying any cracks in the liquid.
- Leak testing (LT): Technicians use leak testing is used to locate defects in a structure or vessel by studying any areas that may be leaking.
Visual Testing Applications
In general, visual testing can be applied to examine a component’s surface condition, analyze the alignment of mating surfaces and check for the presence of leaks.
One application for visual testing involves modern manufacturing. With their tools and non-destructive techniques, a visual inspector can find harmful defects or impurities that will affect how a manufactured material is used in the future. Testing objects before they are sold or used is important, and there are many other fields where the material is tested before public use.
For example, material engineers call on the help of inspectors to gather information about their welding jobs’ workmanship, survivability and material deterioration. This application is crucial to society because these inspectors look at materials commonly used by the public, such as stairs and guard rails. By examining these components, inspectors can ensure that safe parts make it to the market so that clients and consumers alike can benefit from well-made, high-quality materials.
Other industries that use visual testing include:
- Aerospace
- Oil and gas
- Troubleshooting and research
Advantages of Visual Testing
One advantage of visual testing is that it is fairly inexpensive because little to no equipment is needed to perform a visual test. If your operation is running low on funds, consider using visual testing as a first step in ensuring your components are in good shape.
Visual testing is also typically easy to train others in, meaning you can get your operations running more quickly with a shorter training time. This shorter duration is because of the little to no equipment used and the reliance on the naked eye during the process.
Because only a few tools are required for or used during visual testing, this technique is considered a portable testing method. You can do it wherever the component you’re looking at already resides without bringing in big pieces of equipment.
Another advantage of visual testing is that whatever component you’ll be working on won’t require many part preparations — you can visually test the component without doing much tampering with it beforehand. Ultimately, these benefits mean visual testing is a fairly quick and affordable process that numerous businesses can complete without needing extra funds or equipment.
Drawbacks of Visual Testing
Although this is fairly standard practice, one potential drawback of visual testing is that technicians will require the necessary inspector training to be able to conduct it, which will take time and focus. Visual testing will also require individuals to have either good eyesight or eyesight corrected to 20/40.
Visual testing is also a fairly surface-level operation, so an inspector may miss internal defects or large flaws despite carrying out a visual inspection as required. Even if an inspector does their best, they may still miss defects due to human error.
Inspectors must also fill out a report when performing visual testing. In this report, they may accidentally misinterpret flaws or record other errors, which may lead to a flaw being improperly treated during maintenance.
Choose Fujifilm for Your NDT Needs
If you need a VT inspection carried out for your operations, choose the expert NDT technicians at Fujifilm as your partners. When you choose Fujifilm for your NDT needs, you’ll benefit from the following:
- In-house software development capability
- Wide reach across the U.S. with Fujifilm medical services that can troubleshoot similar NDT equipment
- Personalized customer service
- Decreased downtime for inspection
- Reduced unnecessary material waste
- Expedited manufacturing process
- Improved product quality and performance
- NDT equipment that can read X-ray energies emitted from an X-ray source
If you want to know more about us and what we can help you with concerning NDT testing, fill out our online contact form today.