How To Detect Common Defects Found in Aerospace
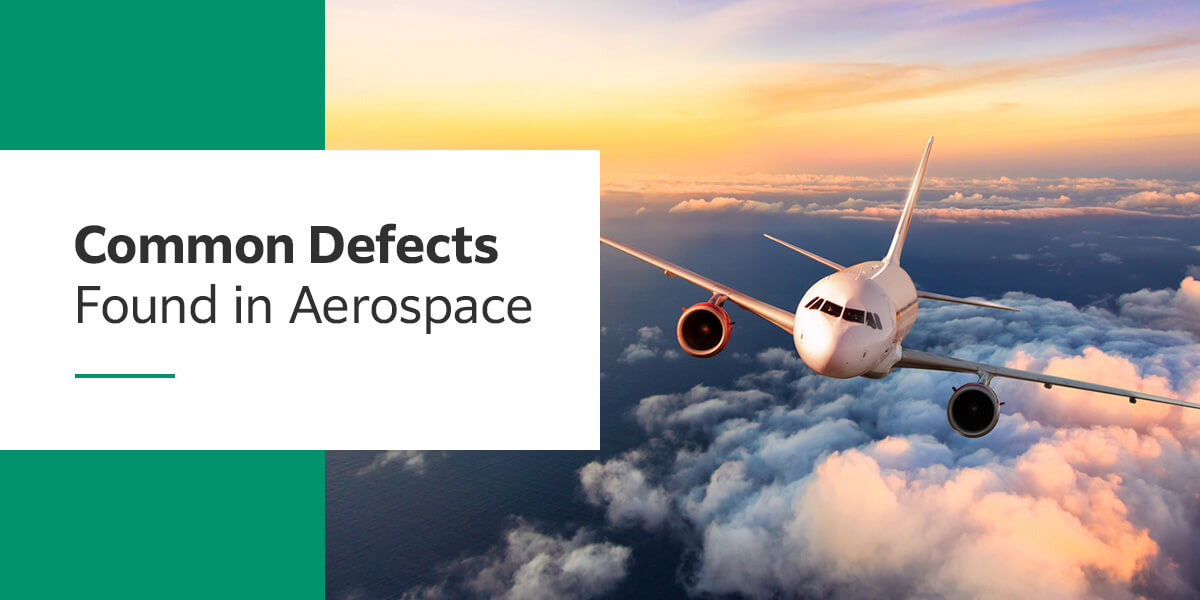
Designing, building and maintaining high-performing, safe and long-lasting aircraft parts is vital for the success of the aerospace industry. Engineers rely on high-quality composite materials to provide lightweight support and tensile strength to endure repeated cycles of ongoing stress. Having a thorough understanding of potential aircraft damage mechanisms can ensure manufacturers produce components that will hold up under repeated use and various stress conditions.
Composite defects are the result of chemical and physical changes that occur within the material’s microstructure. Understanding how the composite materials that are used in aircraft design develop defects is key. This guide to common aerospace defects will explain the causes of composite defects, including fatigue crack nucleation, as well as the different types of cracks and voids that aircraft materials can experience. We’ll also cover the benefits of non-destructive testing in identifying aerospace defects in composite materials.
What Is Damage Nucleation?
In the manufacturing and processing of materials, scientists alter the microstructure of the material to give it certain desirable properties. Altering the microstructure of a material is known as phase transformation, where normally, at least one new phase is formed, giving the material different physical and chemical properties, along with a different structure than the original phase.
Phase transformations don’t occur instantly. Rather, numerous small particles that comprise the new phase begin to form and increase in size until the transformation is complete. There are two distinct stages that occur during the progress of phase transformations: nucleation and growth.
Nucleation is what occurs when the small particles, or nuclei, begin to appear at the start of the new phase. Typically, this consists of several hundred atoms, which are then capable of growing. It’s during the growth stage that nuclei increase in size, effectively causing the particles to leave the original phase.
There are two types of nucleation — homogeneous and heterogeneous. These two types of nucleation are distinguished by the location where the nucleating events occur. In homogeneous nucleation, the nuclei from the new phase form uniformly in the parent phase. During heterogeneous nucleation, the nuclei form at structural impurities, boundaries or other irregularities.
When materials are processed or made, nucleation occurs in a controlled and intentional manner — scientists cause nucleation to happen to achieve a new phase with certain chemical and physical properties. However, nucleation can also occur unintentionally, such as when a material is supercooled or superheated, triggering a phase transformation in the material, and thus, nucleation.
When nucleation occurs unintentionally due to temperature stress or another form of stress, it’s known as damage nucleation. When designing aerospace materials, it’s important to understand the conditions under which damage nucleation occurs. Damage nucleation in composite materials can lead to fatigue cracks that impact the integrity of the material. To design safe and long-lasting aerospace materials, materials engineers need to understand how to prevent or mitigate damage nucleation that leads to cracks and voids in the material.
One of the most significant contributors to damage nucleation is dislocation absorption that occurs at the material’s grain boundaries or surfaces. Dislocations occur during heterogeneous nucleation, whereby stress accumulates at locations with structural inhomogeneities. Compared to homogeneous nucleation, heterogeneous nucleation has a much lower rate of change in free energy. This means its threshold of energy to overcome during the nucleation process is much smaller than for homogeneous nucleation. As a result of having a lower rate of change of free energy, heterogeneous nucleation occurs more readily than homogeneous nucleation.
Heterogeneous materials, such as composites, are more susceptible to damage nucleation. Pressure changes and temperature fluctuations are more likely to cause damage nucleation in composite materials compared to non-composite or traditional materials.
Understanding the conditions under which damage nucleation occurs in composite materials is highly critical to predicting when stresses will occur that cause breakage in the material’s microstructure.
What Are Fatigue Cracks?
Fatigue cracks are one of the primary causes of damage to structural components. Materials that undergo repeated cycles of use experience varying degrees of cyclic stress. After a certain number of cycles, the material will fatigue or become tired, failing at a particular stress level that’s below the material’s real strength. The fatigue causes the material to develop cracks due to fiber breakage, which occurs during damage nucleation.
Fatigue cracks are hard to see, making them extremely dangerous, particularly in critical applications, like aerospace. When materials engineers design composites, they calculate the fatigue life of a component. This is the number of cycles required to cause the initiation of a fatigue crack in a material and to propagate the fatigue crack to a critical size and then to eventual failure.
Scientists measure fatigue stress in three stages:
- Initiation: Fatigue cracks commonly initiate at the free surface level or near a stress location. They will develop wherever there are discontinuous localizations within the material’s microstructure. During this process, the metal in the composite actually becomes work-hardened, meaning it loses its ability to plastically deform in this localized area and instead strengthens. As its plastic deformation limit is reached, the discontinuity in the material forms a crack.
- Propagation: Once a crack has already been initiated, the material will continue to undergo cyclic stresses, which repeats the process over again. Slowly, the micro-crack grows and eventually becomes a threat to the structural integrity of the material.
- Final rupture: After continued crack propagation, the material will eventually weaken so much that it will reach a final point of rupture. The final rupture from fatigue typically occurs suddenly, leading to a catastrophic failure of the material. The fracture surfaces of the broken material are usually smooth with undetectable levels of plastic deformation.
Understanding the stages of fatigue cracks is vital to engineering composite materials that are longer lasting and withhold their structural integrity under specific cyclic stresses. Knowing how composites reach fatigue can help scientists better predict how long a component will actually last under typical conditions.
Types of Fatigue Cracks
Material failure is almost always caused by fatigue. However, the underlying causes leading to fatigue are much more varied. There are at least five primary causes of fatigue, each of which has its own properties and conditions that initiate cracking. Knowing how each of these types of fatigue arises is essential in designing and testing composite materials for the aerospace industry.
Below are the most common types of fatigue failure leading to aerospace defects:
- Mechanical fatigue: Mechanical failure occurs due to an issue with the mechanical material strength of the composite. Manufacturer defects, weak weld points, poor material choice and design flaws are all potential issues that lead to mechanical failure.
- Creep fatigue: One of the most common aircraft damage mechanisms is creep fatigue, which occurs when there is an accumulation of cyclic or thermal stress. These stresses deform the material slowly over time, leading to the creep of fatigue that gradually deforms the material. Eventually, the deformity becomes so severe that the part fails.
- Corrosion fatigue: When chemical reactions occur between composite materials and factors in the external environment, it can lead to corrosion fatigue. Oxidation changes the physical properties of the material, making it more brittle and at risk of cracking under the fatigue of cyclic stress.
- Thermo-mechanical fatigue: Another potential cause of composite defects is thermo-mechanical fatigue, which is a combination of mechanical, creep and corrosion fatigues. When extreme temperatures cause gradual fatigue and get exposed to environmental factors, then the materials become more prone to cracking, resulting in aircraft defects in composite materials.
- Fretting fatigue: When aircraft composite materials come into repeated contact, fretting fatigue occurs. The continuous wear between two separate surfaces leads to increased stress and eventual fatigue cracks.
No matter which type of fatigue cracks occur, each variety can be minimized, prevented and accounted for with proper composite materials engineering and testing to reduce the risk of aircraft defects.
What Are Voids?
Voids are dead space in the material. These unoccupied pores contain gas instead of solid material. Considered imperfections, voids are a type of composite defect that develops during the manufacturing process. While fatigue cracks are due to repeated cycles of use and other stresses the material endures, voids are a different type of composite defect that affects aircraft parts. While fatigue crack nucleation happens during the first stage of phase transformation from the parent phase to the new phase, voids occur as a result of a third phase transformation that’s unintended.
Materials engineers aim to reduce the presence of voids in composite materials. Voids are undesirable aircraft defects that can inhibit the mechanical properties of the composite. With reduced mechanical properties, composite materials have a shorter lifespan and can lead to catastrophic failures of aerospace components.
Voids can lead to heterogeneous nucleation that can eventually initiate and propagate a fatigue crack. They are essentially an additional and problematic triggering cause of fatigue crack nucleation, eventually leading to failure in the composite.
Because voids lead to potentially dangerous catastrophic failures, they are considered aircraft defects that need to be avoided. Materials scientists have developed a few different techniques for preventing voids from developing during the composite manufacturing process. One of the main ways to prevent voids during manufacturing is to use a vacuum method combined with a heated and pressurized system that physically removes voids. This method only works on certain types of composites, particularly ones with lower viscosity, which prevents the voids from moving throughout the matrix.
Scientists continue to study and investigate the causes of voids and the best ways of removing them during the manufacturing process. A combination of control and simulations can help materials scientists better understand how to approach the problem of voids in composite materials.
Types of Aerospace Voids
How voids form during the materials manufacturing process depends on the type of materials that make up the composite. In particular, the viscosity of the matrix resin is what determines the type of void the composite forms.
Highly viscous resins are more likely to produce voids in the finished composite material. When fibers are particularly packed together tightly, then it’s difficult for the resin to penetrate the space in between each fiber. Therefore, any gas that’s currently between the fibers that doesn’t get covered by the resin will never be pushed out. Instead, the gas will be effectively cured in place as the material gets finished, creating a permanent void in the material.
In addition to voids related to resin viscosity, there are also types of voids related to manufacturing errors. One example is when voids occur due to the temperature applied to cure the material being too low. If the resin is cured at a low temperature, then the material will not degas enough to eliminate the air pockets. Conversely, if the temperature is too high during curing, then the resin will quickly turn gelatinous, and the air pockets won’t have enough time to diffuse out of the material. In either situation, the voids occur due to collected air in the resin, leading to irregularities in the microstructure.
Detecting Aerospace Defects With Non-Destructive Testing
The ability to effectively detect aerospace defects in composite materials is of critical importance. Detecting composite defects, such as finding fatigue crack nucleation and voids, is an important part of all aircraft scheduled maintenance programs. One of the most effective and economical ways of finding defects is through non-destructive testing or NDT.
In materials engineering, it is a common practice to push materials to their absolute limits in order to discover the loads and stresses that cause materials to fail. However, in manufactured products, such as aircraft, engineers can’t destroy materials to find defects. Instead, they must find innovative ways to test their materials while keeping them intact. Non-destructive testing is one method of achieving this balance.
Aircraft defects, such as voids and fatigue cracks, are invisible to the naked eye, making it difficult to detect them. With non-destructive testing, engineers can find cracks and irregularities in the composite material using a few different methods. One of the ways that engineers discover cracks and other aircraft defects is through radiography using X-rays or gamma rays. Radiography produces high-quality imaging that can help manufacturers and technicians detect aerospace defects within composite materials that would otherwise be invisible.
Non-destructive testing using radiography is a highly efficient process, being able to be conducted effectively and quickly with a high level of accuracy. Because it doesn’t directly impact or alter the aerospace parts, it also keeps the manufacturing, testing and maintenance costs low.
Work With FUJIFILM for Your Non-Destructive Inspection Services
To improve your organization’s ability to accurately detect aerospace defects and foreign object debris, you need reliable, cost-effective testing methods. Radiography is a highly accurate and affordable method of non-destructive testing that can identify aircraft defects, including voids and fatigue cracks. For non-destructive testing technology you can trust, choose FUJIFILM for both digital radiography and conventional X-ray methods.
Discover more about FUJIFILM’s non-destructive testing services for the aerospace industry. We offer non-destructive testing systems as well as training programs. With decades of experience as leaders in imaging products, FUJIFILM provides the aerospace industry with an innovative way to identify defects and maintain high structural integrity in all composite materials to reduce the risk of failure. Contact us today to learn more about our non-destructive testing solutions.